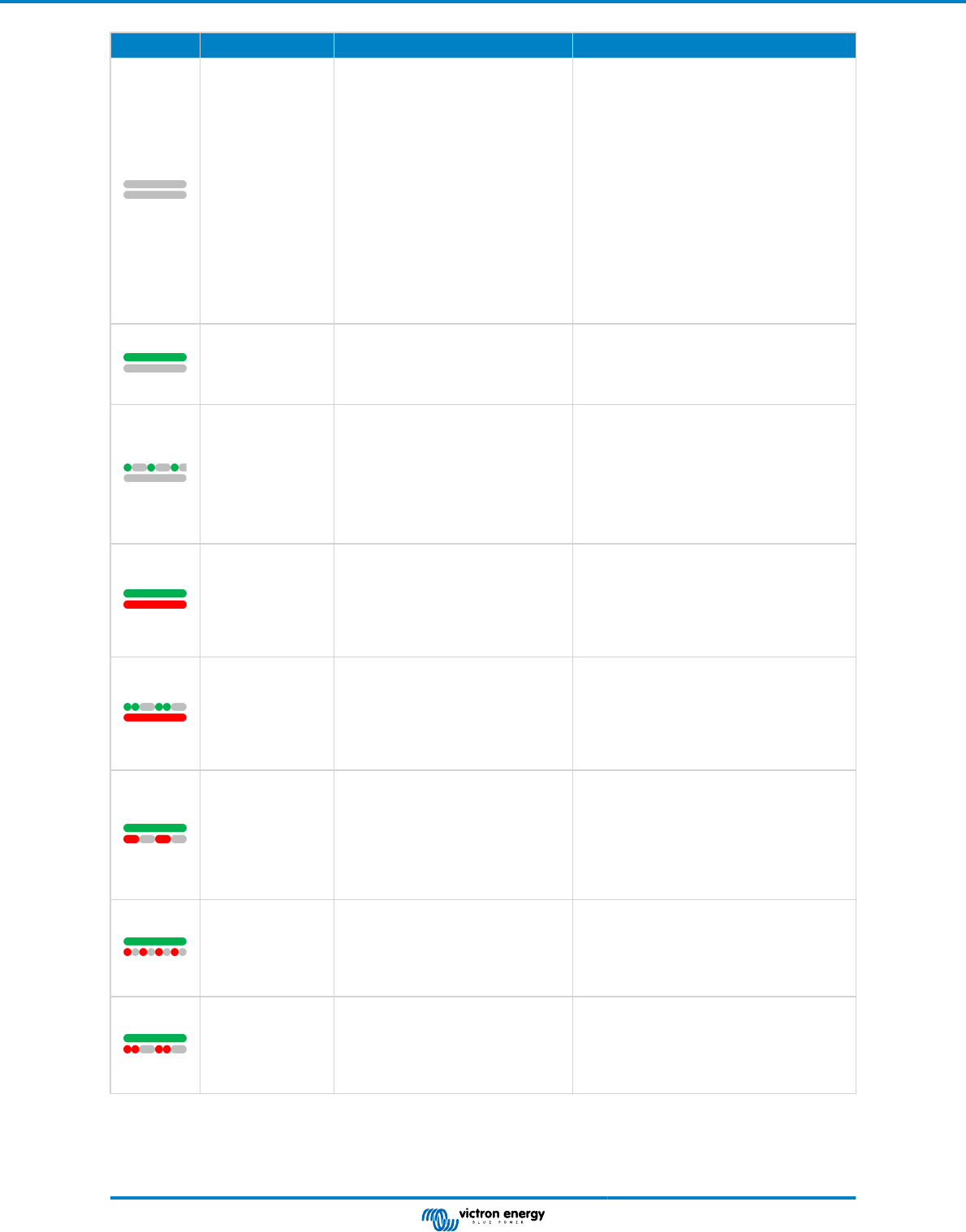
LEDs LED behaviour Operational mode Troubleshooting
Green POWER
LED off.
Red ALARM LED
off.
The inverter has been switched off,
either directly or via its remote on/off
connector, or the inverter is not
powered.
Check the ON/OFF/ECO switch: it should
be in ON position or in ECO position.
To check if the inverter is operational, turn
the switch to OFF and then to ON.
If not operational, check the following:
• Check the remote on/off connector. Is the
wire loop in place or is the remote switch
or remote panel switched on?
• Check the DC cable connections and
external fuses. Do you measure battery
voltage at the inverter battery connection?
• If the internal fuse is blown, the inverter
has to be returned for service.
Green POWER
LED on.
Red ALARM LED
off.
The inverter has been switched on
and is operational.
n/a
Green POWER
LED blinking slow
with a short pulse.
Red ALARM LED
off.
The inverter has been switched to
ECO mode and is in "search" state.
In other words, the inverter load is
lower than the "Wake up power"
setting. the inverter sends a search
pulse at regular intervals to check if
a load has been connected or has
been turned on.
If the inverter keeps switching on and off
while there is a load connected, the load
may be too small compared to the actual
ECO mode settings. Either increase the
load or change the "wake up power" setting.
Green POWER
LED on.
Red ALARM LED
on.
Overload warning.
The inverter is indicating that the AC
load is larger than the inverter rating
and that if this situation continues,
the inverter will switch off due to an
overload alarm
Reduce the AC load
Green POWER
LED blinking with
a fast double
pulse.
Red ALARM LED
on.
Overload alarm.
The inverter has shut down due
to prolonged overload and will no
longer automatically restart.
Remove the cause of the overload and then
restart the inverter by switching it off and
then back on again.
For more information also see the
Protections and automatic restarts [23]
chapter.
Green POWER
LED on.
Red ALARM LED
blinking slow.
Low battery voltage warning.
The battery voltage has dropped
below the "Low battery alarm"
voltage. Should the battery voltage
drop any further, the inverter will
switch off on a "Low battery voltage
alarm".
Charge the battery and/or turn AC loads off.
Also check if all battery cable connections
have been tightened. Do the battery cables
have a sufficient thickness, is the battery
full and is the battery still in good working
order?
Green POWER
LED on.
RED ALARM LED
blinking fast.
High Battery voltage warning.
The battery voltage is too high.
Should the battery voltage increase
any further, the inverter will switch
off on a "High battery voltage alarm".
Reduce the DC input voltage, check if the
battery voltage is correct and if the battery
bank is wired correctly. Also check if there
perhaps are faulty or incorrect chargers or
equipment with a faulty charge regulator.
Green POWER
LED on.
Red ALARM LED
blinking with a fast
double pulse.
High temperature warning.
The internal temperature is too high.
If the temperature increases any
further, the inverter will switch off on
a "High temperature alarm".
Reduce the AC load and/or move the
inverter to a better ventilated area.
SUN Inverter Manual
Page 21 Operation